Crushing magnetite rock before milling is a crucial step in the mineral processing industry, particularly in the beneficiation of iron ores. The primary purpose of this process is to reduce the size of the ore particles to a level where the valuable minerals can be liberated from the waste rock. Here are the detailed reasons and benefits of crushing magnetite rock before milling:
-
Liberation of Minerals:
- Objective: The main goal of crushing is to liberate the valuable minerals from the surrounding waste rock. Magnetite, being an iron ore, is often found in conjunction with other minerals and gangue materials.
- Process: By crushing the rock, the magnetite particles are freed from the surrounding matrix, making it easier to separate them during the subsequent milling and beneficiation processes.
-
Increased Surface Area:
- Objective: Crushing increases the surface area of the ore particles.
- Benefit: A larger surface area allows for more efficient chemical reactions during the beneficiation process, such as flotation or magnetic separation. This can lead to higher recovery rates of the valuable minerals.
-
Improved Efficiency of Milling:
- Objective: Milling is an energy-intensive process, and the efficiency of this process can be significantly improved by pre-crushing the ore.
- Benefit: Smaller particles are easier to grind, which reduces the energy consumption and wear on the milling equipment. This can result in cost savings and increased throughput in the milling circuit.
-
Enhanced Separation Techniques:
- Objective: Effective separation of magnetite from the gangue material is essential for producing a high-quality concentrate.
- Process: Crushing the ore to a finer size allows for more effective use of separation techniques such as magnetic separation, gravity separation, or flotation. These techniques rely on differences in physical or chemical properties between the magnetite and the waste material.
-
Consistent Feed Size:
- Objective: Providing a consistent feed size to the milling circuit is important for maintaining stable operating conditions.
- Benefit: Crushing the ore to a uniform size ensures that the milling process operates more smoothly and efficiently, reducing the likelihood of operational issues such as blockages or uneven wear on the milling equipment.
-
Preparation for Downstream Processes:
- Objective: The crushed ore must be prepared for further processing steps, such as concentration and pelletizing.
- Process: Crushing ensures that the ore is in the optimal size range for these downstream processes, which can improve the overall efficiency and effectiveness of the beneficiation plant.
In summary, crushing magnetite rock before milling is a critical step in the mineral processing chain. It ensures the liberation of valuable minerals, increases the surface area for chemical reactions, improves the efficiency of the milling process, enhances the effectiveness of separation techniques, provides a consistent feed size, and prepares the ore for downstream processing. All these factors contribute to the overall efficiency and cost-effectiveness of the beneficiation process, ultimately leading to higher recovery rates and better-quality iron ore concentrates.
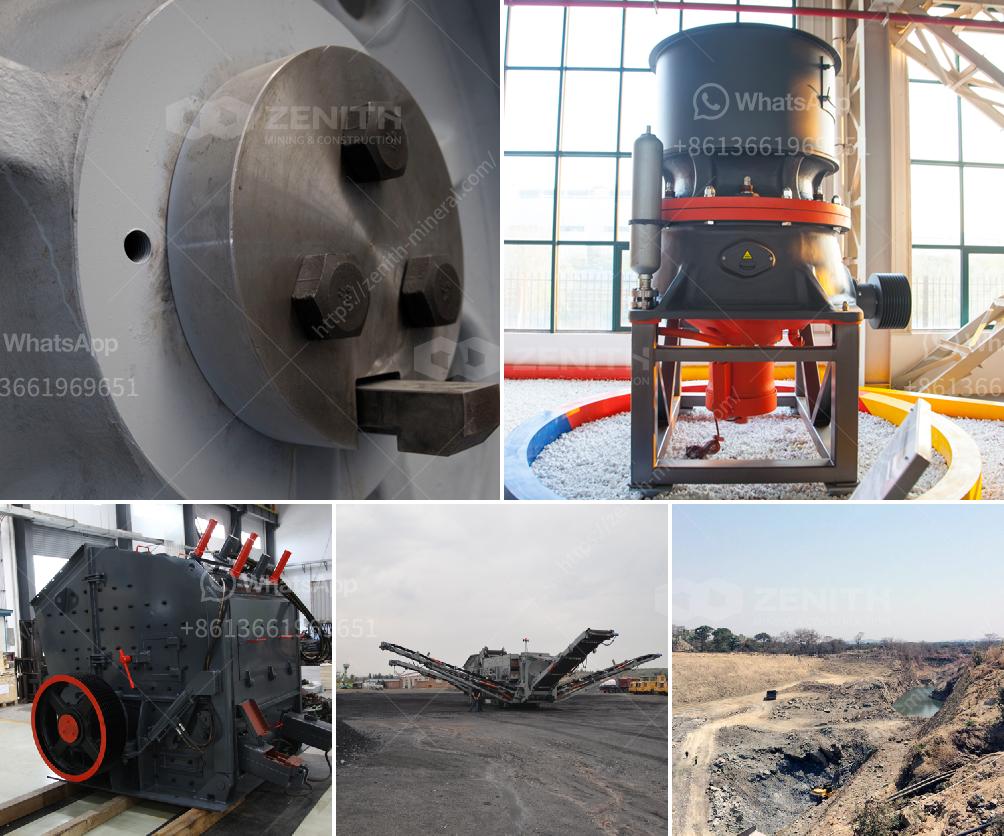